23/10/2024
How IoT and bespoke software are driving the manufacturing revolution
In June 2024, manufacturing accounted for 8.8% of total UK economic output and 7.0% of employment - which is around 2.6 million jobs. In the first quarter of 2024, output grew by 1.2% compared to the previous quarter, increasing manufacturer confidence to its highest level since 2022.
When we think of the manufacturing industry, we may envisage human production lines and large-scale industrial machines. However, according to European Business Magazine, embracing technological advancements is essential for the future of the industry.
Industry 4.0, the driving force in the modern manufacturing industry
At its core, the fourth industrial revolution - a phrase first introduced by a team of scientists developing a high-tech strategy for the German government - is about connecting machines, devices, and systems through smart technologies, enabling real-time data sharing, advanced automation, and highly flexible manufacturing processes.
The Internet of Things (IoT) refers to the network of physical devices, sensors, and machines embedded with software and connectivity features that enable them to communicate and share data.
For manufacturers, the rise in IoT means a shift in the way they operate, focusing on data-driven decision making, increased efficiency, and enhanced productivity.
Key benefits include:
- Reducing downtime
- Optimising supply chains
- Improving product quality
- Developing more agile, responsive operations that can quickly adapt to changes in demand
IoT devices provide the backbone for a truly connected, intelligent manufacturing facility. However, the unique requirements of each manufacturer make bespoke software solutions essential for fully leveraging these IoT capabilities.
What are the IoT trends in manufacturing?
In the manufacturing sector, IoT devices are becoming integral to operations, providing real-time insights into production processes and machinery performance. Some commonly seen and emerging applications of IoT in the manufacturing sector include:
Smart sensors
These are devices that monitor everything from equipment temperature, pressure, and vibration to energy consumption and environmental conditions within the factory. They provide data that manufacturers can use to prevent machine failure and optimise resource use.
Industrial robots
Robots enhanced with IoT capabilities are used to streamline processes like assembly, packaging, and warehousing. IoT allows them to communicate with other machinery, improving coordination and efficiency.
Connected equipment
Machines connected to the IoT ecosystem can share data on performance and wear and tear, providing actionable insights that reduce downtime and extend equipment lifespan.
Predictive maintenance
Through IoT, manufacturers can monitor machine health in real-time, predicting potential failures before they occur. This data-driven approach minimises unplanned downtime, reduces repair costs, and extends the life of machinery.
Supply chain optimisation
IoT enables real-time tracking of raw materials, components, and finished goods, improving transparency throughout the supply chain. Sensors can monitor inventory levels, reducing stockouts and overproduction, and ensuring timely deliveries.
Automation and autonomous systems
IoT devices enable greater automation across manufacturing lines, from autonomous vehicles transporting goods to fully automated production processes. This not only reduces the reliance on human intervention but also improves safety and precision.
Bespoke software is at the heart of Industry 4.0
While off-the-shelf software can manage basic operations, bespoke software development is essential for manufacturers looking to fully harness IoT and achieve Industry 4.0 goals. Here's how custom software solutions enable innovation in the manufacturing sector:
1. Tailored to specific operational needs
Each manufacturing facility has unique requirements, from the types of machinery used to the specific workflows in place. Bespoke software solutions can be developed to integrate with existing infrastructure and IoT devices seamlessly. This allows manufacturers to collect, analyse, and use data that is highly relevant to their processes, unlike generic solutions that may provide too much unnecessary information or fail to capture key data points.
2. Enhanced data integration and analysis
One of the biggest advantages of IoT is the ability to collect vast amounts of data from various points in the production process. Bespoke software platforms can integrate data from multiple sources—IoT devices, enterprise resource planning (ERP) systems, and supply chain management tools—into a centralised dashboard. This not only enables manufacturers to monitor operations in real-time but also to run advanced analytics and predictive models that help drive decision-making.
3. Predictive maintenance and machine learning
Predictive maintenance, powered by IoT data, is one of the key innovations of Industry 4.0. bespoke software uses machine learning algorithms to analyse sensor data, detect anomalies, and predict when a machine is likely to fail. This prevents costly breakdowns and ensures equipment operates at optimal efficiency. A bespoke solution can be fine-tuned to monitor specific machines and operational conditions, delivering more accurate predictions than a one-size-fits-all approach.
4. Scalable and flexible solutions
As manufacturing operations evolve, so do the requirements for IoT and software. Custom solutions offer scalability and flexibility, ensuring that software can adapt to new machines, additional data points, or shifting operational goals. Off-the-shelf solutions may lack this adaptability, making bespoke development crucial for manufacturers seeking long-term innovation and efficiency.
5. Improved security and compliance
The manufacturing sector faces increasing concerns around data security and compliance with regulations such as GDPR. Bespoke software solutions offer a higher level of security, allowing businesses to implement advanced encryption, access controls, and data privacy measures tailored to their specific needs. This is particularly important when handling sensitive operational data or proprietary manufacturing processes.
- Maximising ROI on IoT Investments
Manufacturers investing in IoT devices need a software platform that can optimise the use of those devices, extracting relevant data and driving actionable insights. Custom software ensures that the full potential of IoT investments is realised, from predictive maintenance to automation.
- Agility in a competitive market
In the fast-evolving world of manufacturing, being able to quickly adapt to new technologies, processes, and market demands is key. Bespoke software provides the flexibility needed to implement new innovations rapidly and stay ahead of competitors.
Working with industry-experienced developers
Manufacturing is unlike other industries in its reliance on highly specific machinery, processes, and regulatory standards. This means it’s ideal to work with software developers who have experience in the manufacturing sector. Experienced developers understand the complexities of manufacturing environments and can design solutions that integrate seamlessly with existing systems and technologies with minimal disruption.
David Ritchie, founder and director at Propel Tech, comments:
“Bespoke software developers with manufacturing expertise can foresee potential challenges—such as interoperability between different IoT devices or the impact of downtime—and can design software that addresses these issues proactively. Their knowledge of manufacturing best practices ensures that bespoke solutions align with industry standards and compliance regulations, reducing risk and improving operational reliability.”
Propel Tech has long standing relationships with leading manufacturing businesses throughout the UK, making possibilities happen through a range of software services, from bespoke development and ongoing improvement and maintenance, to testing, database services, system integration and web applications. Discover more about our work.
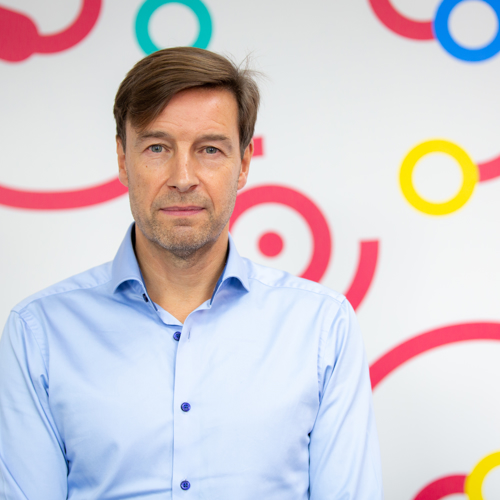
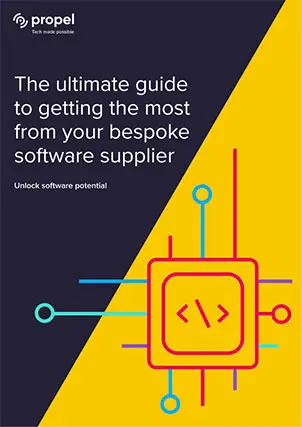